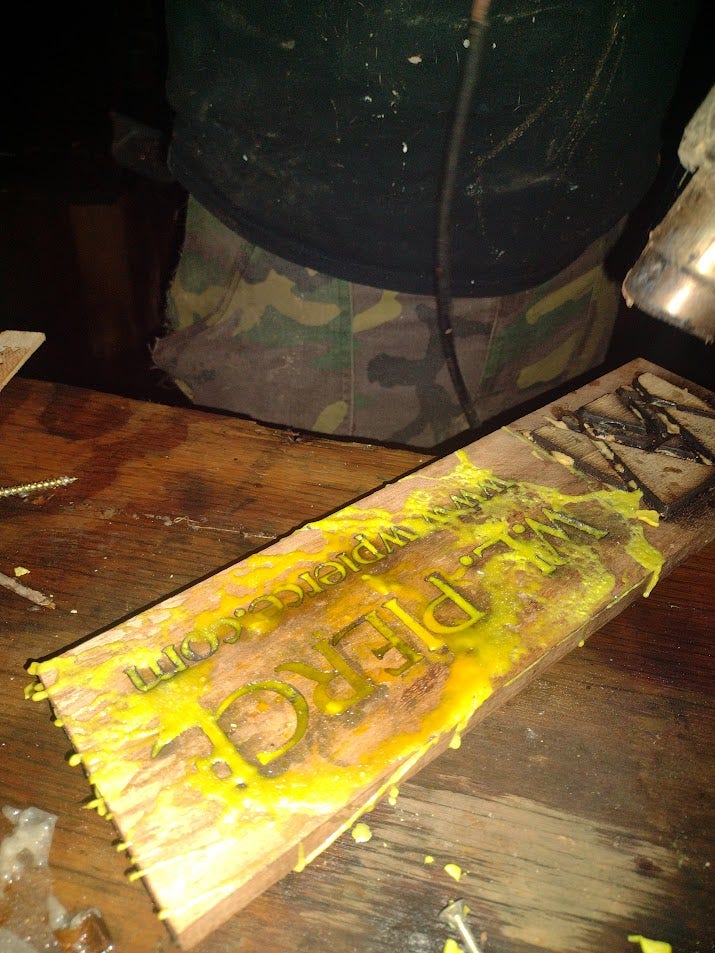
Sulfur inlay is a sort of obscure historical process that was only ever heavily used by a generation of two of Amish, a substitute for fancier traditional materials like ivory that weren’t really available to an 18th-century luddite in rural Pennsylvania, but still has some distinct advantages over modern epoxy fillers if you’re a smalltime craftsperson shooting for a more traditional/natural effect and don’t mind everything being some shade of yellow-white. It’s also extremely cheap and simple to get started with, so I’ve been experimenting with it as an option for more elaborate designs I really don’t want to cut marquetry for.
Sulfur powder is commonly available as a fertilizer and chemical reactant, you just melt it to a watery consistency at a hair over 200°F and pour over whatever you want filled, where it’ll rapidly recrystallize and (crucially) expand as it cools, locking it firmly in place. Once cast it’ll last as long as the underlying material does, and if you ventilate well it’s downright eco-friendly compared to most plastics – I wouldn’t sprinkle it on a salad, but you could apparently ingest it all day and not get much more than an upset stomach, and the salad greens would love it. It cleans up much quicker and cleaner than epoxy does – and if you don’t get sawdust and crap in it, which will stain it a blotchy dark color fairly quickly, whatever you scrape off or don’t use can be melted down and reused indefinitely.
Now the downsides: it’s sulfur, the medieval shorthand for what hell smells like. Standards for industrial odors have declined considerably since those days, and I don’t have much of a sense of smell anymore anyway so I don’t much care, but it’s decidedly antisocial, and you’ll be smelling like it for a while afterward. If you manage to light it on fire (which doesn’t take a whole lot) it burns with an invisible flame and gives off some very nasty toxic fumes, which react with water (like the kind your eyes and lungs are covered with) to produce sulfuric acid. To head this off the Amish would apparently bake it slowly outdoors in a sealed clay vessel – we have the advantage of induction burners with no exposed combustion, but you still want to keep an eye on temperature and keep it right around its melting point. And make sure the stuff you’re getting is actually pure sulfur, not some weird fertilizer mix; my first try I used some ebay mystery powder with some kind of absurdly low-combustion-point additive and teargassed the lot of us.
Unfortunately it tends to form bubbles as you pour it out, which I’ve combatted with some success by remelting the surface with a heat gun, but as you can see below it’s still not suitable for large expanses of perfectly even inlay. Will see eventually if a vibration table can fix this, but so far it’s got a strong potential provided you’ve got an outdoor space and local cops don’t care if it looks and smells like you’re cooking meth in your yard.
